Advantages of Gas-Assisted Injection Molding
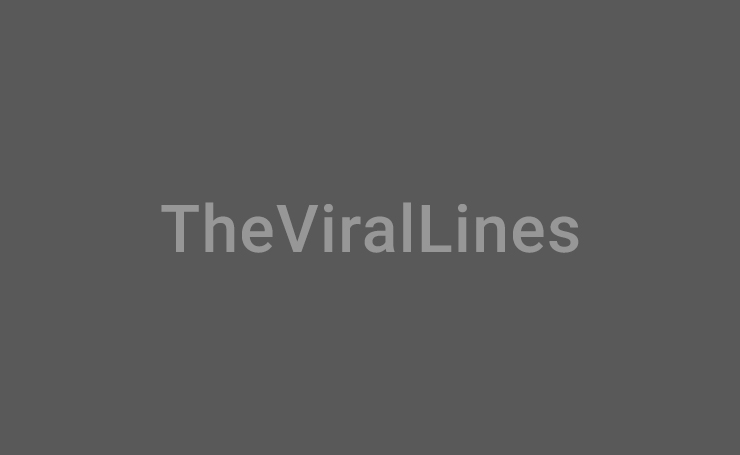
Gas-assisted injection molding is a specific type of injection molding that is a popular choice for manufacturing high-performance plastic parts. The benefits of gas-assisted injection molding include the fact that it can increase tool life and produce higher-quality parts.
Gas Assisted Injection Moulding is a highly technical form of injection Moulding, that uses both plastic and gas (usually nitrogen) to fill an injection mold under pressure.
The main benefit of this manufacturing process is its ability to form hollow parts in the cycle time of injection molding machines.
The basic process of Gas Assisted Injection Moulding is unsurprisingly very similar to regular injection molding. The extruder barrel of an Injection molding machine melts down raw pelletized plastic material, then injects this into an injection mold but only up until the mold is about 70% full.
Then from a separate entry point, pressurized gas is injected into the mold as the part is cooling. This forces the still molten plastic up against mold walls, where it cools and hardens into your plastic product.
The pressure is released from the gas, and then the mold is ejected like a regular injection molded part.
What is the principle of gas-assisted injection molding?
Gas-assisted injection molding works by injecting pressurized nitrogen gas into the interior of a mold, forcing the molten plastic material against the outer surfaces of the mold.
Gas can be simply used to ensure constant contact of the molten plastic against the tool whilst cooling to produce better-looking parts, or be used to fill the core of the plastic and also improve its mechanical properties.
The gas-assisted injection molding process:
-
Plastic polymer powder or granules are fed into the machine and heated.
-
The molten polymer is then injected into the mold.
-
Nitrogen gas enters the chamber and pressurizes the molten plastic into the sides of the mold.
-
The gas is released once the polymer cools after being held against the sides of the mold.
Advantages
-
Less plastic material needed (material savings)
-
Reduced part weight (in some cases up to 40%)
-
Decreased cycle time
-
Increased part strength and rigidity
-
Reduced warpage and distortion
-
Improved part appearance (eliminates sink marks and surface blemishes)
-
Reinforces ribbed parts
-
Increased design options for complex parts, reducing multiple part assemblies, and metal to plastic conversions
-
Enables use of smaller plastic injection molding presses
In gas-assist plastic injection molding, the pressurized gas follows the path of least resistance and displaces the plastic material in the thicker areas of the part, leaving hollow sections for reduced material use and part weight, yet not compromising part appearance or functional performance.
With gas assist molding, localized gas pressure within the mold results in better packing of the plastic which reduces warpage, shrinking, surface blemishes, sink marks, and internal stress.
Gas assist injection molded plastics generally make for stronger and more aesthetically pleasing parts.
Why is gas injection molding used?
The popularity of gas injection molding (GAM) is due to it providing additional strength, lightness, and feature definition to plastic part design.
So for intricate, lighter designs, it is a preferred choice. Less polymer is used to make the product, as the final result is hollow, meaning up to 50% of the material is saved. Shrinkage and warping are also eliminated with GAM.
Key takeaway
Gas-Assisted Injection molding offers a range of advantages in comparison to Injection Moulding. Firstly, there is the ability to mold hollow parts, but this hollowness also is a major weight saving, which in turn also saves on material costs.
The hollow interior also lessens and sometimes removes flow lines as the plastic is now under constant pressure from the gas.